The AI Revolution: Transforming Manufacturing Efficiency
The industrial revolution has been a driving force behind efficiency in manufacturing for the past century. However, with the advent of digitalization and the rise of artificial intelligence (AI), we are now experiencing a new revolution that is reshaping the way Original Equipment Manufacturers (OEMs) approach manufacturing.
Harnessing the Power of AI in Manufacturing
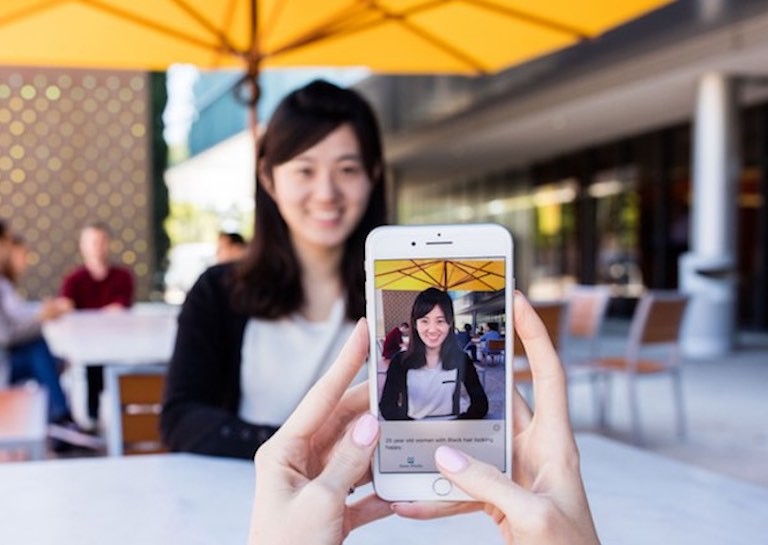
Companies like Siemens have utilized AI to enhance the operational efficiency and product quality of their machines. By leveraging existing data from machines and implementing predictive maintenance strategies, significant time and resource savings have been achieved.
Unlocking the Potential of Data
Previously, valuable machine data was often discarded. However, Siemens recognized the opportunity to collect this data at a relatively low cost. By gathering 11 million data sets, each with 40,000 data points for each component, they were able to implement effective predictive maintenance measures. This allowed them to detect potential failures in advance, preventing production line breakdowns and minimizing losses.
Improving Quality and Throughput
AI has also played a vital role in predicting the quality of components early in the production process. Siemens, for example, utilized AI algorithms to identify which parts were at risk of failure, eliminating the need for costly X-ray tests on all components. The result? A reduction of 30% in X-ray tests, a 100% quality rate, and a substantial capital investment saving.
Learning from Defects
Not only did Siemens identify defective parts through data analysis, but they also delved deeper to understand the root causes of defects. This information was then fed back into the product line, driving continuous improvement in quality.
The Added Value of AI in Manufacturing
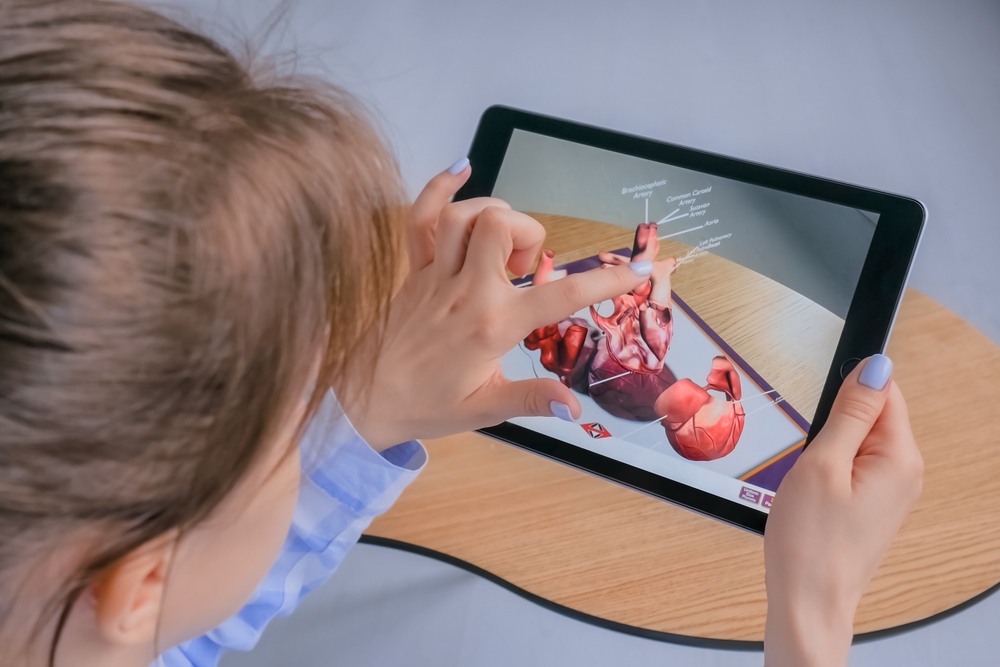
Despite the success stories, some OEMs still question the value of AI in their already efficient factories. However, industry experts argue that AI is not just a standalone technology but rather a transformative approach to manufacturing.
Scaling and Revolutionizing Manufacturing
According to Indranil Sircar, CTO of Manufacturing Industry at Microsoft, AI can revolutionize manufacturing by extending the level of detail and insight across the entire production line and supply chain. The implementation of AI in agile factories typically occurs in three phases:
Phase 1: Connect and Gain Visibility
Phase 2: Analyze and Predict
Phase 3: Optimize and Automate
In this phase, factories are connected and data is ingested to provide visibility into operations. AI plays a crucial role in contextualizing this data and creating a digital twin of the factory.
Data analysis is performed to identify causes and impacts. AI, machine learning, and simulation techniques are utilized to predict outcomes and improve productivity.
In the final phase, AI drives optimized operations and facilitates the transition towards autonomous systems, resulting in increased efficiency and productivity.
The Enhanced Capabilities Enabled by AI
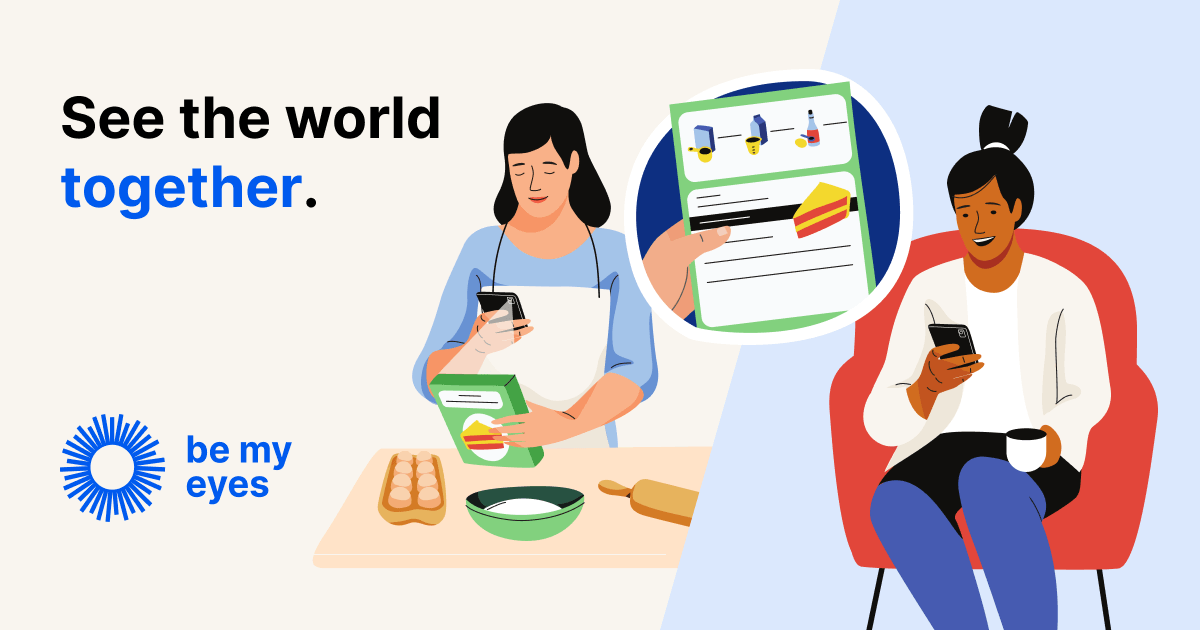
Artificial intelligence empowers manufacturing with a range of advanced capabilities:
Enhanced Predictive Maintenance
Quality Assurance and Testing Efficiency
Predictive Analysis for Demand and Supply
Process Optimization and Automation
By leveraging AI, predictive maintenance strategies can be implemented, allowing for proactive identification of potential failures and minimizing downtime.
AI algorithms can analyze data and selectively apply thorough testing only to components at risk of failure, reducing testing time and costs without compromising quality.
AI can analyze historical data, market trends, and external factors to predict demand and optimize supply chain management, ensuring timely production and reducing inventory costs.
Through AI-powered process optimization, inefficiencies and bottlenecks can be identified and addressed, leading to improved productivity and reduced waste.
Conclusion
The AI revolution is transforming the manufacturing industry, offering significant benefits in terms of efficiency, quality, and cost savings. By harnessing the power of AI, OEMs can revolutionize their operations, optimize processes, and drive productivity. Embracing AI as a way of working allows manufacturers to unlock new potential and gain a competitive edge in the dynamic global market.
FAQs
1. How does AI improve manufacturing efficiency and quality?
AI enables predictive maintenance, early defect detection, quality prediction, and process optimization, leading to improved efficiency and higher product quality.
2. Can AI be implemented in existing manufacturing facilities?
Absolutely. AI can be integrated into existing factories to enhance operations and drive efficiencies without requiring a complete overhaul of the system.
3. Does implementing AI require extensive sensor deployment?
Not necessarily. Existing data from machines can often be utilized to benefit from AI without the need for additional sensors.
4. What are the cost savings associated with AI implementation?
AI implementation can result in significant cost savings by reducing downtime, minimizing quality issues, optimizing testing, and improving overall productivity.
5. How can AI revolutionize the manufacturing supply chain?
AI can analyze data and market trends to predict demand, optimize inventory levels, and streamline supply chain management, ensuring efficient production and timely delivery.